耐火浇注料施工六大要点 直接关系窑炉运转质量
发布时间:2024/8/23 17:36:04
耐火浇注料是窑炉施工中常用的耐火材料之一,其施工质量直接影响到窑炉的运转质量和使用寿命。为了确保施工效果,需要严格遵循以下六大要点:
1. 材料选择与质量控制
材料选择:根据窑炉的不同部位和工作环境,选择合适的浇注料。例如,高温区通常选用高铝质、刚玉质或镁铝尖晶石质浇注料,而低温区则可选用轻质浇注料。
材料质量:确保使用的浇注料符合国家标准或设计要求。特别要注意材料的化学成分、粒度分布、耐火度和抗热震性等关键指标。
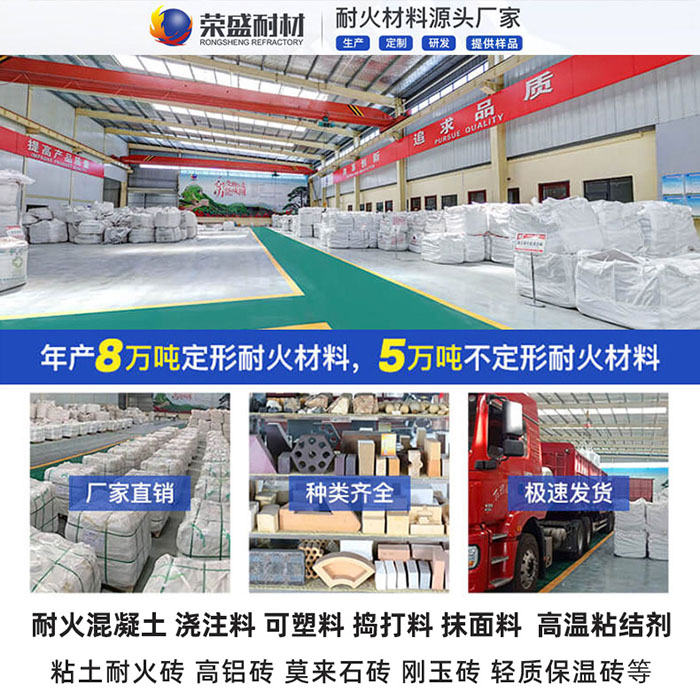
2. 配料与搅拌
严格按照比例配料:浇注料的配料过程须严格按照设计比例进行。水灰比、外加剂的使用量要严格控制,以保证浇注料的性能达到设计要求。
搅拌均匀:浇注料在使用前需要充分搅拌,确保材料的各组分分布均匀。搅拌时间一般为3-5分钟,搅拌不充分可能导致浇注料强度不足或不均匀。
使用清洁的搅拌设备:搅拌设备应保持清洁,避免旧料残渣混入新料中,影响浇注料的质量。
3. 模具安装与检查
模具设计:模具的设计和安装应考虑到窑炉的实际形状和施工需求,确保浇注料能够充分填充模具,并在凝固后易于拆卸。
模具检查:在浇注料施工前,须仔细检查模具的牢固性和密封性,确保模具无漏浆现象。模具内表面应涂抹脱模剂,以便于后续的拆模工作。
加固和定位:模具需要进行加固和定位,特别是在大型或复杂结构的窑炉施工中,以防止在浇注过程中模具移位或变形。
4. 浇注与振捣
连续浇注:浇注料的浇注应尽量连续进行,以避免分层现象的发生。分层会导致结构强度不均匀,影响窑炉的整体性能。
合理振捣:在浇注过程中,使用振动棒进行振捣,确保浇注料的密实性,排除气泡和空隙。振捣时要注意力度适中,过度振捣可能导致材料分离,过少则会有气泡残留。
层层浇注:对于较厚的浇注层,应分层浇注和振捣,每层厚度一般控制在20-30厘米,确保每一层都充分密实。
5. 养护与拆模
湿养护:耐火浇注料浇注完毕后,应立即进行养护。通常采用湿养护或覆盖塑料薄膜的方式,保持表面湿润,防止浇注料因失水过快而产生裂纹。养护时间一般为24-48小时,具体时间根据材料和环境条件而定。
拆模时间:拆模时间应根据浇注料的硬化程度来决定。一般在浇注完成后24小时即可拆模,但要避免过早拆模导致浇注料的边缘损坏。
养护环境控制:养护期间,应避免阳光直射和强风吹拂,保持施工区域的湿度和温度稳定,促进浇注料的均匀硬化。
6. 质量检验与修补
外观检查:拆模后应对浇注料的外观进行检查,确保表面平整,无蜂窝、气孔、裂缝等缺陷。
强度测试:必要时进行强度测试,以验证浇注料的实际性能是否符合设计要求。可以通过回弹仪或钻芯取样等方式检测浇注料的强度。
及时修补:如果发现局部有缺陷或强度不足,应及时进行修补。修补材料和工艺应与原浇注料保持一致,确保修补部位的质量。
通过严格执行上述六大要点,可以确保窑炉耐火浇注料施工的质量,为窑炉的长期稳定运行提供可靠保障。
- 上一篇:整体性耐火材料施工规范需要注意什么?
- 下一篇:没有资料
行业动态