耐火材料在炉外精炼钢包熔池损蚀过快因素
发布时间:2022/12/15 15:36:32
耐火材料在炉外精炼钢包熔池损蚀过快因素,炉外精炼是炼钢厂对钢水进行深脱氧、硫,去除夹杂物和合金化的主要冶炼过程,请看详细内容。
考虑LF精炼钢包不同部位的侵蚀介质不同,主要分为渣线区和熔池区。钢包渣线区域由于受到氧化物熔渣的剧烈侵蚀,通常采用的是含碳量在12~18wt%的MgO-C砖,由于熔渣对渣线耐火材料的熔损较快,一般在使用过程中至少需要更换一次渣线。
熔池区耐火材料在精炼过程中受钢液的侵蚀,钢包浇完钢热修之前需要倒渣,倒渣面耐火材料主要受到熔渣的化学侵蚀和物理冲刷,熔池区耐材可选用的材质有镁铝碳材质、铝镁碳材质或者无碳铝镁材质。在服役过程中熔池区耐材处于钢包的中下部,更换施工难度大,同时经济上性价比一般比较低,所以很大程度上熔池区使用寿命决定了整个钢包的寿命。
耐火材料的损毁机理是一个相对比较复杂的问题,熔渣性质、操作温度、耐材组成以及冶金条件都会影响其侵蚀过程,现场钢包衬的损毁更加是温度场、钢/渣流场以及化学侵蚀综合耦合后导致的结果。因此探明熔池区耐火材料的局部损毁机理不仅是耐火侵蚀机理的科学探究,同时相关结果对工程现场也有很强的指导意义。
1、情况调查
某钢厂180t转炉钢包,钢包拆包过程中发现钢包熔池部位12点方向的熔池砖残厚明显比周边的砖残厚低(见图1),限制了包龄的进一步提升,见表1。该厂的基本条件是:冶炼环境为LF精炼,比例100%,生产钢种大部分为铝镇静钢,炉渣碱度比较高,见表2;钢包内部结构主要为透气砖分布在5点和7点方向(见图2),精炼时电极插入钢包内,位置在1点、2点和6点位置(见图3)。
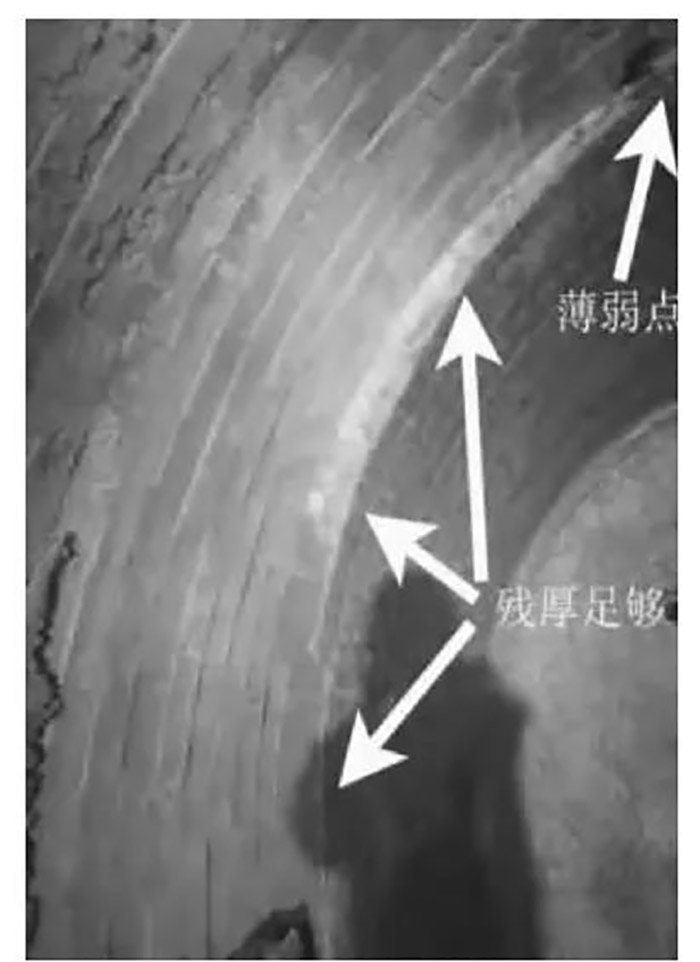
图1:拆包时熔池砖厚度情况 (mm)
众所周知,钢包产生薄弱点的常见位置有三个:①电极附近。电极产生的高温导致渣/钢液和耐火材料的反应加快。②透气砖附近。透气砖吹通后加快钢液对耐火材料的冲刷。③倒渣面。在一次钢包周转结束的时候,需要将包内剩余的钢液和钢渣倒出,倾倒过程中倒渣面受到钢渣和钢液的冲刷和侵蚀。而在该现场的薄弱部位并不是这三个常见部位,所以研究它是很有意义的。
从现场取熔池薄弱方向和非薄弱方向的用后砖(如图4、图5所示),有效厚度分别为160 mm和60 mm。从图中可以看出,非薄弱方向熔池砖表面有渣层存在,薄弱方向熔池砖几乎没有渣层;平行于热面方向,非薄弱方向熔池砖表面有两道裂纹,里面已经填充了渣。接下来我们对取回来的砖进行分析,确定其损毁机理。
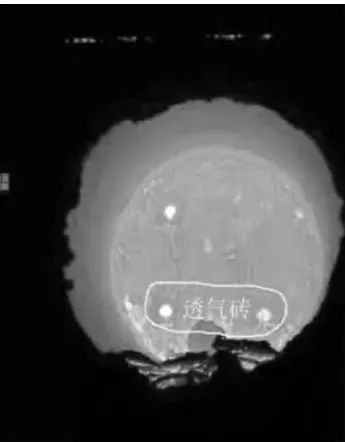
图2:钢包-透气砖位置现场图
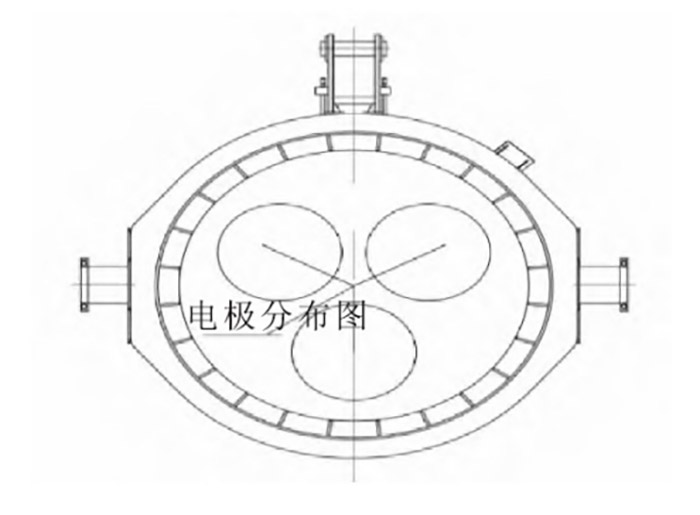
图3:石墨电极在钢包内的相对位置示意图
2、用后砖检测和分析
1)检测方法和过程
距热面每隔25mm切一块样品(25mm×25mm×25mm)进行物理和化学性能检测,热端部分进行显微结构分析。
2)用后砖样物理化学分析
表3给出了距热面不同距离样品的物理指标。可以看出,在0~25 mm部位,两方向熔池砖显气孔率和体积密度相差不大,但薄弱方向样品的体积密度略高于非薄弱方向的体积密度;30~55 mm区间,薄弱方向样品的体积密度2.80 g/cm3明显高于非薄弱方向砖的体积密度2.74 g/cm3,显气孔率14.8%明显低于非薄弱方向砖的显气孔率16.2%。可以说距离热面相同位置,来自薄弱点的样品具有较高的体积密度和较低的显气孔率,这从侧面表明薄弱点方向的熔池砖具有较低的渣渗透层或者脱碳层。
表3:距离热面不同距离样块的显气孔率和体积密
根据距热面不同距离样品的化学指标可以看出,随着距离热面越远,CaO含量逐渐降低;距离相同的试样对比,非薄弱点方向样品中的CaO含量要高于薄弱点方向样品;原砖层的CaO含量应该在1.3wt%左右,其中5点方向非薄弱点的砖在距离热面30~55mm时,CaO含量为1.57%,大于1.3%,这表明非薄弱方向的熔池砖的渣渗透层深度至少为25mm。
3)显微结构分析
图6是5点方向用后熔池砖的显微结构图。可以看出,5点方向用后熔池砖热面部分明显分为四层,渣层、反应层、脱碳层和渗透层;渣层厚度3.4mm,反应层2.7~4.6mm,脱碳层厚度3.4mm,距离热端远的地方氧化钙含量也比较高,该部位渣的渗透深度很大。
从表5的化学分析看,整个25 mm的样品均存在渣渗透。5点方向熔池砖表面的反应层比较厚,颗粒和基质烧结在一起,较为致密,强度高,阻碍了氧气和渣中氧化物对砖的进一步氧化,同时具有一定的抗冲刷性能。表5给出能谱分析,在反应层中形成了镁铝尖晶石,这表明高碱度渣中,在高温下氧化铝和镁砂形成尖晶石是高温物相,能够很好地保护钢包砖,避免进一步侵蚀。
图6给出了12点方向用后熔池砖的显微结构。渣层厚度0.6 mm,反应层和脱碳层总厚度约为0.6 mm,渗透层厚度约为2.5 mm。与5点方向用后包壁砖的显微结构不同,薄弱点方向渣层、反应层、脱碳层、渗透层很薄,很快达到原砖层,这也和前面表3和表4中物理化学分析一致;渣和砖形成的反应层不连续不致密。
表6给出了各部位化学成分,可以看出,随着距热面距离的增大,砖中的氧化钙含量迅速降低,区域5时氧化钙含量已经达到原砖层化学指标,砖的渗透深度比较小。综上可知,5点方向用后熔池砖有明显的反应层和脱碳层,且反应层较为致密连续,能够阻碍渣和氧对砖的进一步损毁和钢水冲刷;12点方向用后熔池砖表面不能形成稳定的反应层,不断和外界空气或者渣接触,新的反应层很快被冲刷掉,不断露出新的脱碳层反应,是一个侵蚀-氧化-侵蚀/冲刷循环交替过程。这也和众多文献中对用后渣线砖侵蚀情况叙述一致。
致密反应层的产生可能和现场的操作有关。钢包浇钢完毕后,从连铸平台下来,需要将剩余的钢包渣和钢液倒出,在倒渣过程中,倒渣面被渣覆盖,化学侵蚀加剧,但对砖起到了防热震效果,同时高碱度渣和砖形成了较致密和连续的反应层,阻碍了空气和渣对砖的进一步侵蚀。12点方向在浇钢过程中随着渣液面下降附有薄薄的一层渣,浇钢完毕后受到空气氧化和热震作用,不能形成反应致密层,在下一轮使用过程中受钢液冲刷,导致反应层被冲刷掉,终导致该部位的砖侵蚀过快。
3、结论
本文针对某钢厂精炼钢包熔池砖局部侵蚀过快的现象,系统分析钢包熔池区不同部位用后残砖的侵蚀形貌,得出如下结论:
钢包的冶金操作过程是导致LF精炼钢包局部熔损过快的主要原因,倒渣面受钢渣覆盖,形成了较致密的反应层,阻碍了空气和渣的进一步侵蚀,也能提高钢包砖的抗冲刷性能,非倒渣面耐火材料局部异常侵蚀主要是因为钢包砖与渣之间的反应层不致密,结构疏松,在下一轮冶炼过程中更容易被钢水冲刷损毁,伴随着冶金精炼操作的循环过程,侵蚀-氧化-侵蚀/冲刷循环交替过程是含碳炉衬损毁的主要机理。
基于以上分析得出结论:①提高非倒渣面耐火材料的致密性,增加钢包砖与渣之间的反应层的致密程度。②增强耐火材料的高温抗折强度,提高钢包砖的抗冲刷性能。③提高非倒渣面耐火材料的抗氧化性,降低冶金操作过程的氧化程度。
以上就是全部内容,希望给大家有所帮助。
- 上一篇:石灰、耐火原料在煅烧竖窑内物料煅烧特性介绍
- 下一篇:耐磨浇筑料在锅炉内衬的应用
行业动态